American Battery Solutions
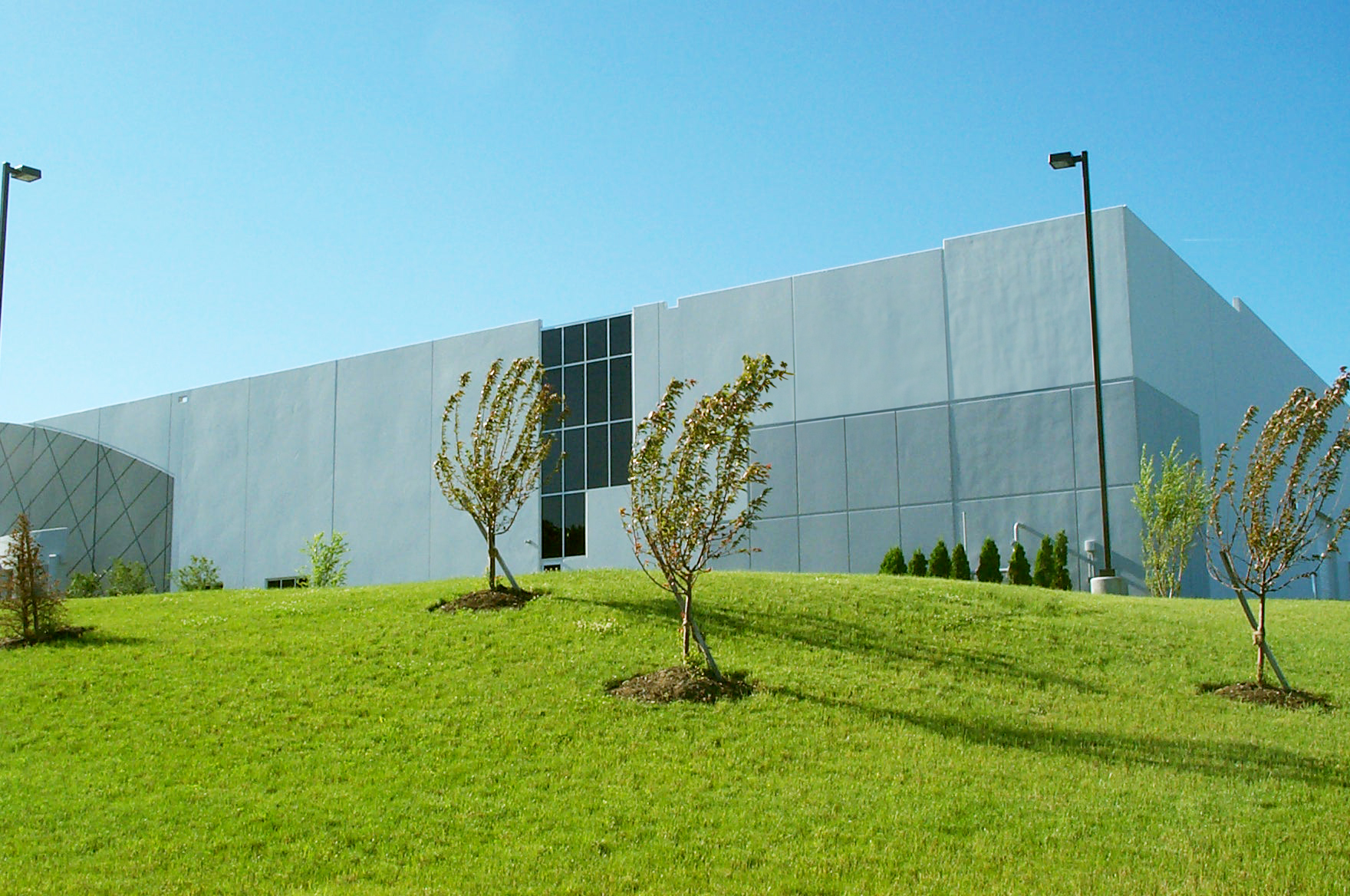
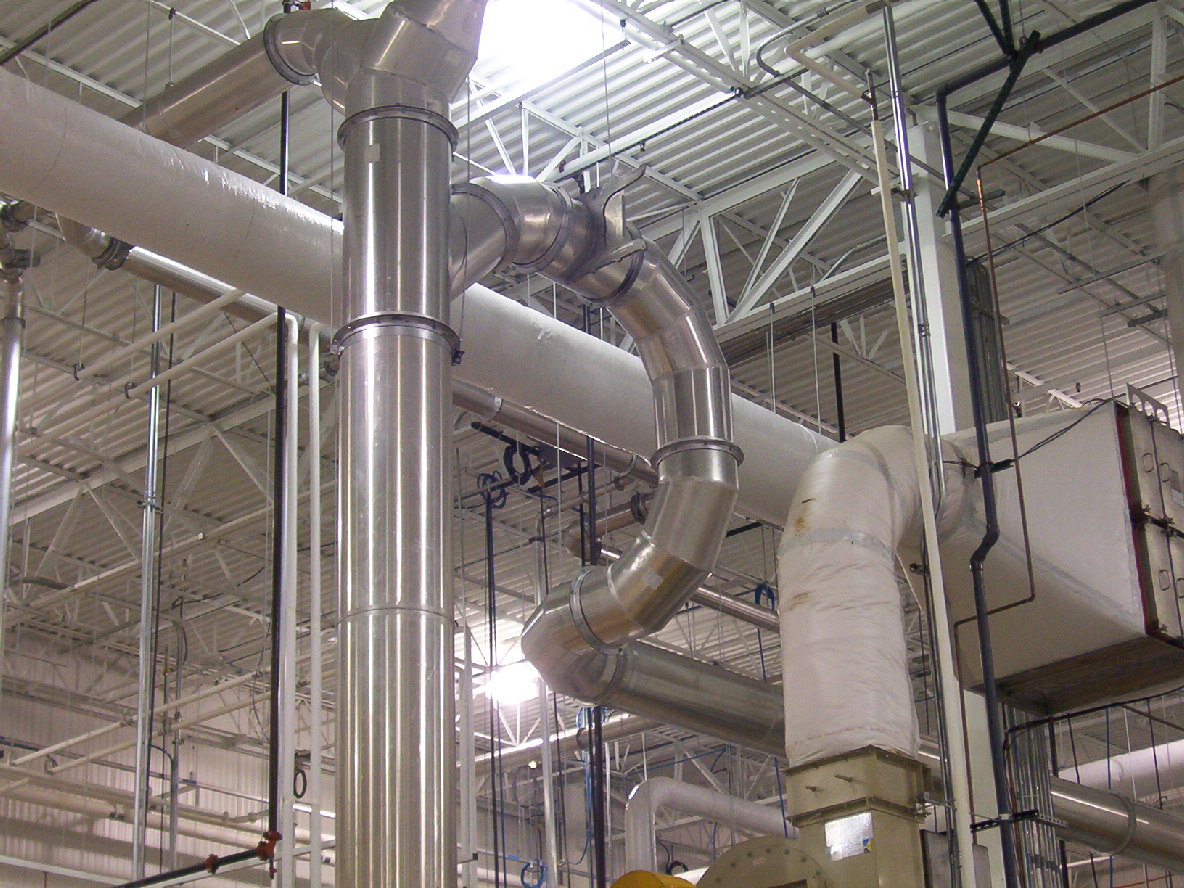
Cost $6,000,000 (original)
$2,000,000 (expansion)
Size 170,000 SF
HEAPY provided facility and process system design for a new 170,000 SF research and automated developmental manufacturing facility for nickel metal hydride (NiMH) battery systems and nickel-plated electrodes for fuel cell energy systems. In 2012-2013, the facility was expanded and converted to Li-Ion production. The facility includes receiving, storage, and handling of power substrates. These are mixed and pasted onto the material to form electrodes.
HEAPY’s scope of work involved a wide range of facility and process design, planning, and mechanical/electrical systems design. Being a high-power density battery developmental center, the facility’s electrical infrastructure was a key element to the overall project. HEAPY designed a total of four, 4000A services at 480V, 3Phase, and 60Hz for the facility and the associated distribution; this equates to a total power density for the facility of 43.3 W/SF.
Additionally, numerous laboratory-grade process utility systems were required to support research and development of various battery types and associated manufacturing processes, including:
- 500-ton capacity water-cooled process chiller water system with a 2500-gallon Thermal Inertia Tank to serve a robotic battery test cell system
- Deionized/Reverse Osmosis (RO) Water System with recirculation pumping and UV Sterilization System
- Multiple High-Pressure Solids Collection Systems with Hoods for Mixing of Powder based electrode material within a Class I, Division 2 NEC Hazardous Classified Space with explosion relief
- Cleanroom Class 100,000 Process Enclosures for pasting equipment with HEPA filter ceiling modules
- Industrial Compressed Air System with three, 1250 SCFM rotary screw air compressors
During the Li-Ion conversion, a series of projects were executed related to handling Li and assembly of Li-Ion battery systems, including:
- Class I, Division 2 – Li storage rooms with intrinsically safe electrical and specialty fire protection systems/detection and needed HVAC systems
- H3 Classified Li-Ion assembled battery units, with specialty fire protection systems and ventilation/humidity control systems
- Cell coating line and curing line: High temperature HVAC curing room, Class I, Division 2 spray coating system with intrinsically safe electrical, specialty fire protection systems and detection, contamination control space with precision T&RH control for coating space
This fast track, design-build project had a building systems budget of $6,000,000 and an additional process utility systems budget of $2,000,000. Final Certificate of Occupancy was granted in just four months and 1 week — two weeks ahead of schedule on this complex project.
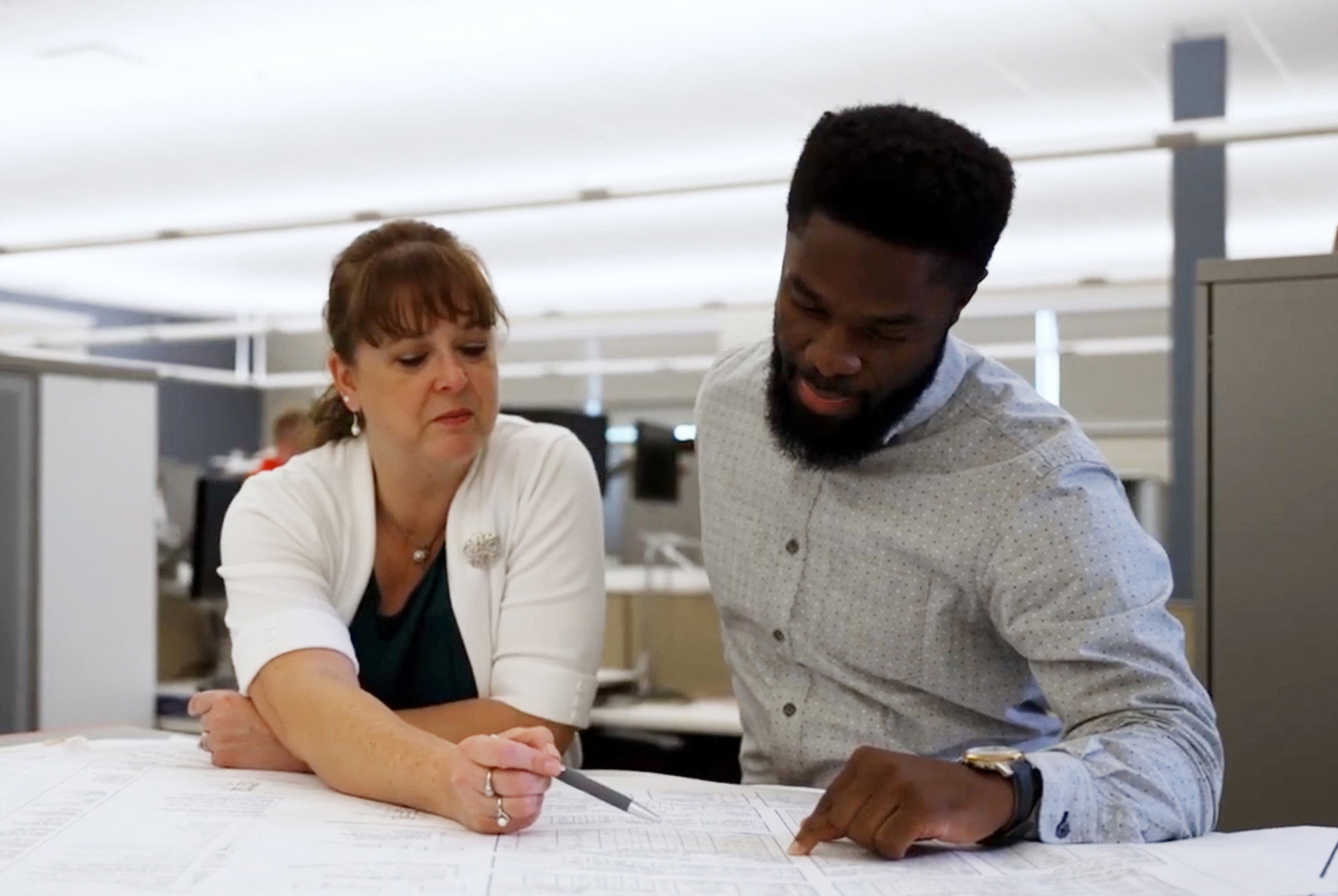
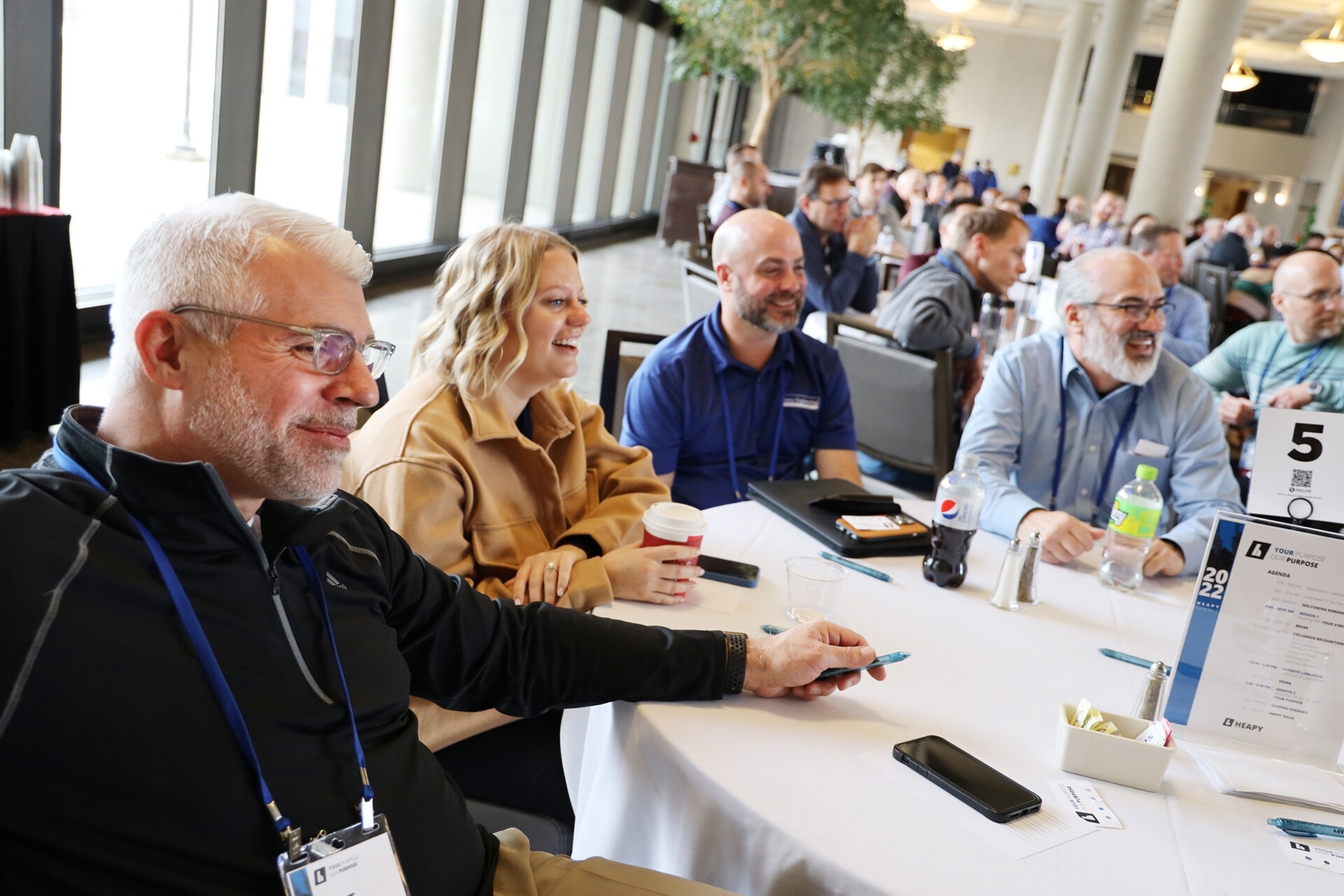