Wright Patterson Air Force Base
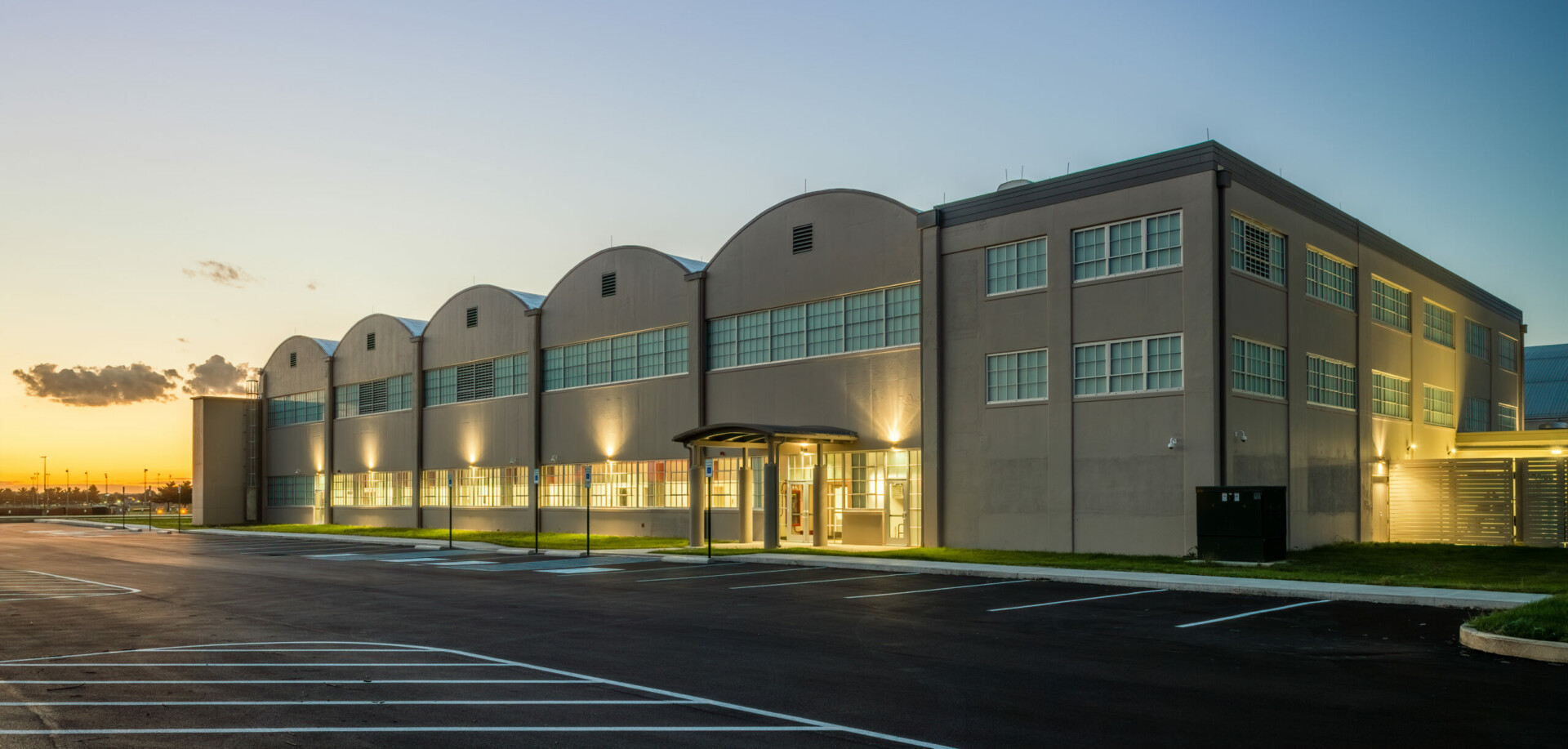
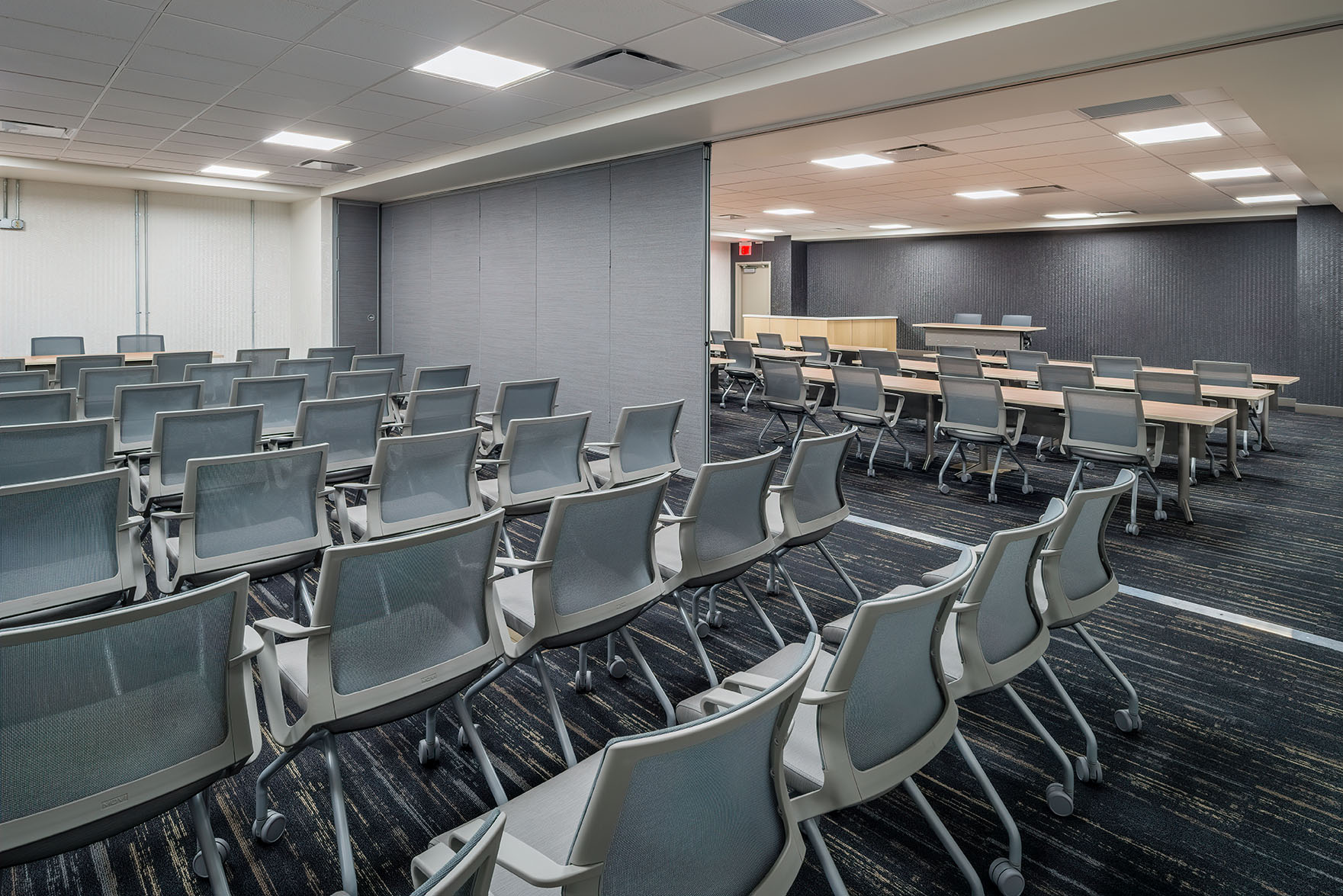
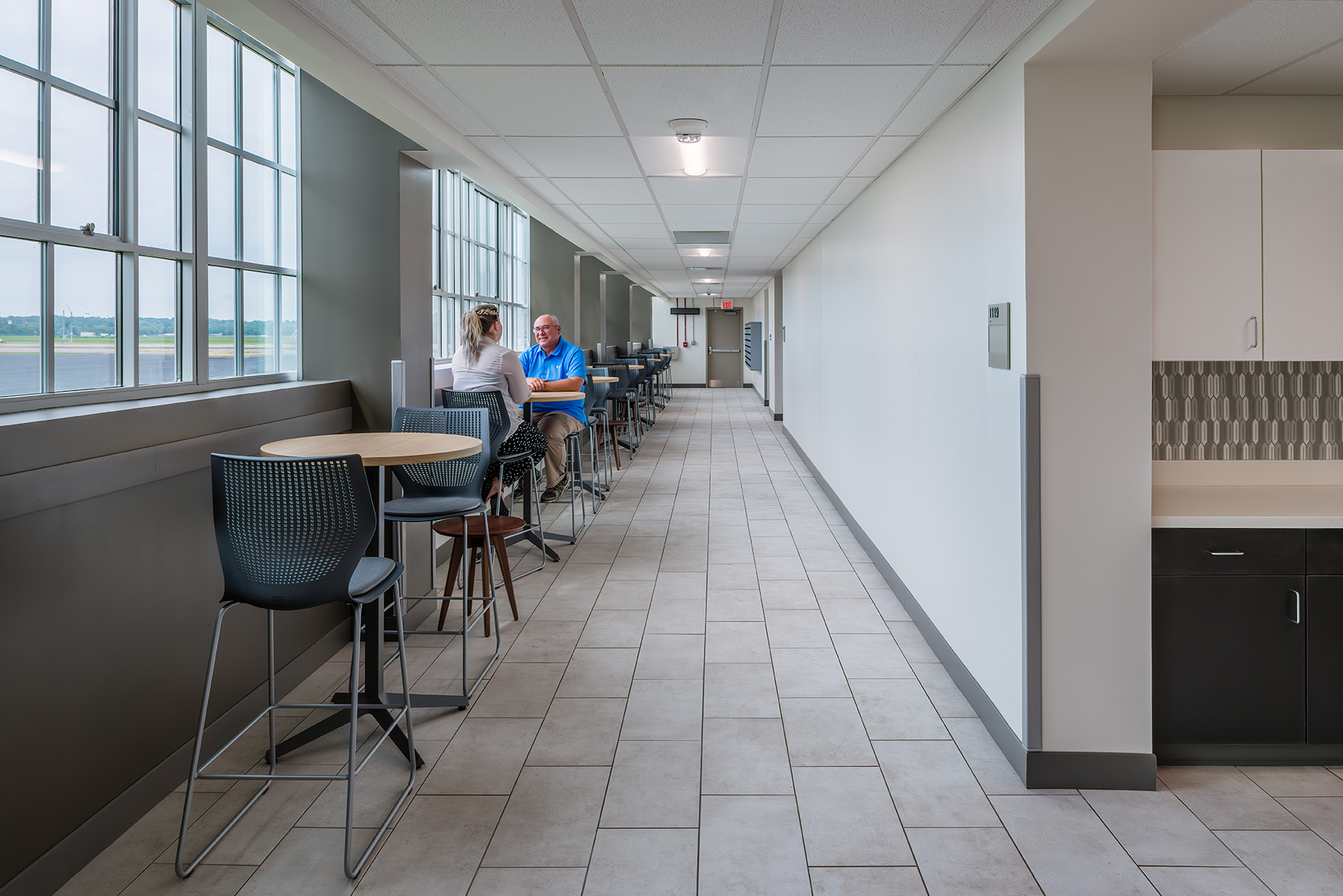
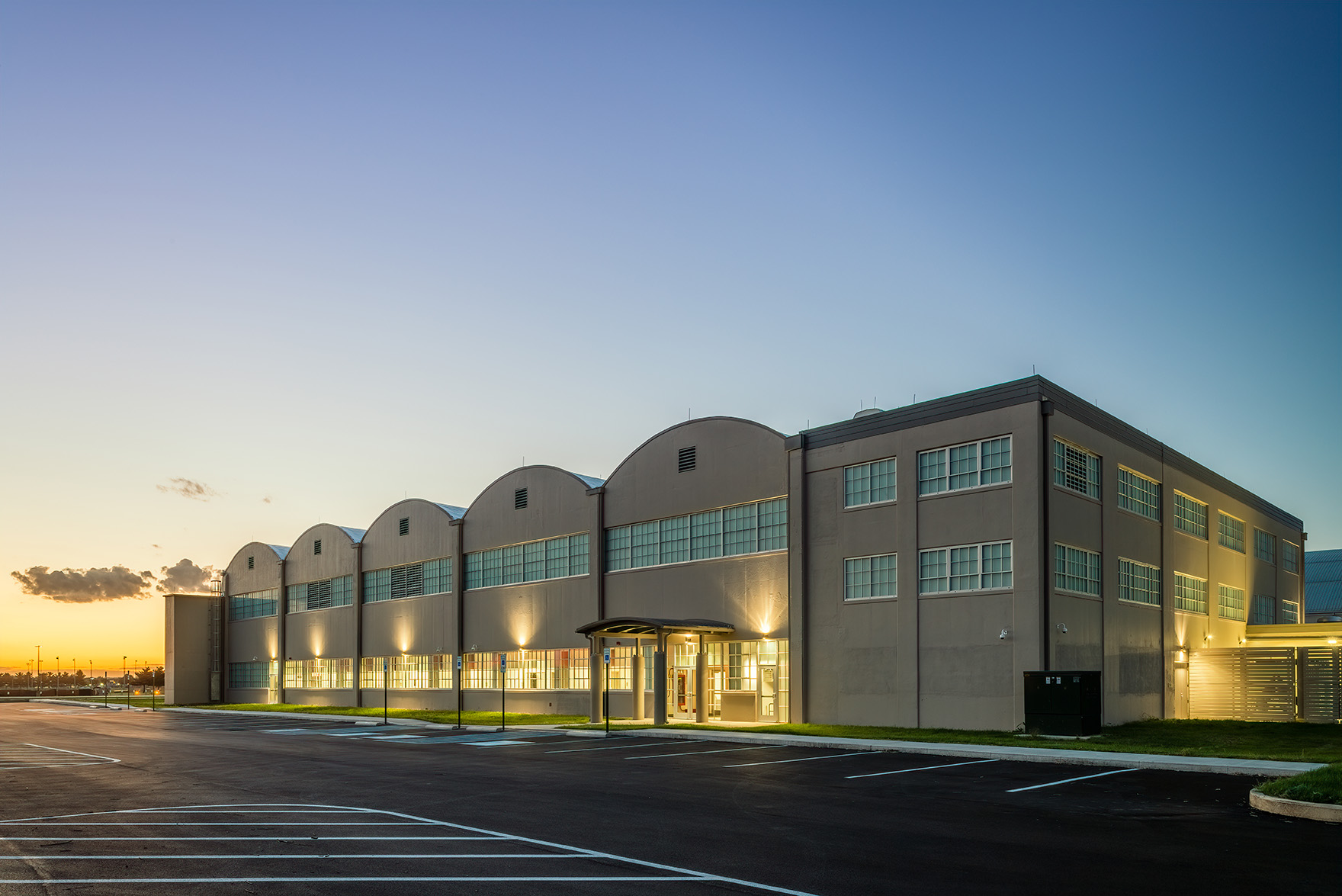
Cost $30,000,000
Size 60,000 SF
HEAPY worked with Air Force Civil Engineer Center, the 88th Civil Engineering Group, Wright-Patterson Air Force Base (WPAFB), and the User through a series of charrettes to prepare preliminary designs, project costs, project requirements, and the Design-Build RFP. This recapitalized a historic 1942 hanger into secure office space incorporating ICD-705 requirements, ATFP, UFC, and WPAFB standards.
This was the initial Air Force project, using the new rules, to modernize a building without MILCON funding and was selected as a 2022 AFCEC Honor Award winning project for design.
Planning Charrette Report (PCR)
The PCR followed the Air Force standard and coordinated with WPAFB staff. It included detailed investigation, testing, evaluation of the structure, ACM, radon and lead based paint testing, geotechnical investigation, and evaluation of existing pavement to convert the historic cast in place concrete hangar with thin concrete barrel vault roof into office space. Through a series of charrettes, the team developed the project requirements including, the program of space requirements, room by room requirements, and space relationships. A DD 1391 was developed for further coordination and approval at higher Air Force levels.
Design Build Request for Proposal
The team developed a detailed design RFP addressing progressive collapse, security, ATFP, utility company coordination, a floor plan coordinating all discipline requirements, and systems for the historic hangar. The concept design developed an efficient and flexible plan which achieved 111 net square feet per person and 148 usable square feet per person. The design met all the requirements for the Cultural Resources Office and SHPO.
Specific Challenges
Throughout the Charrette and RFP generation process, the team had to explore and answer a multitude of conflicting guidance’s as they applied to this specific facility. Specific challenges and solutions included:
- Deconfliction through discussion with WPAFB and higher headquarters concerning the Progressive Collapse requirements in UFC 4-023-03 (Design of Buildings to Resist Progressive Collapse, with Change 3). This applied to both the area where a second story was to be built and the three-story admin section of the building. Both seismic and explosive affects were explored. Complete direction was provided in the DB RFP with associated correspondences and direction by the government eliminating any possible misinterpretation of the contract.
- Complete energy modeling of facility required by UFC 1-200-02 High Performance Sustainable Building design. The team modeled three alternate systems as required and specified the most Life Cycle Cost Effective system as defined by the BLCC program input and analysis to exceed ASHRAE 90.1-2013 by >30%.
- Mission Critical support was required with a dedicated data/server room provided with diesel fire emergency generator for backup power, battery storage, and N+1 redundant and free-cooling capabilities in the event of power/mechanical failure. These systems were separate from the UPS and building chilled water system used for general occupancy of the facility.
- Complete life safety analysis of the complex facility with two- and three-story sections utilizing the Louisville checklist adopted at WPAFB to apply UFC 3-600-01 Fire Protection Engineering for Facilities.
- Application of UFC 4-010-01 DoD Minimum Antiterrorism Standards for Buildings for the large curtain wall hangar doors of the facility and standoff distances around the facility.
- Facility is secure and most of the facility is required to comply with Intelligence Community Directive ICD 705. This required thorough direction to the many spaces surrounding the administrative and technical areas to specify a compliant facility.
- Hazardous material identification and abatement plan included a complete and thorough investigation of the facility for asbestos, lead paint, PCB, and radon, which was completed with a report provided in the RFP. The radon investigation provided determined that no radon mitigation measures were required after consulting with WPAFB. This saved an estimated $30,000 in construction costs. Direction and back-up information such as test results and WPAFB direction were provided in the RFP.
- Technology design required coordination to determine the communication requirements with three separate computer networks, server room, secure spaces with access requirements, separation and security requirements, and life safety limitations. Coordination meetings resulted in a security design in the RFP due to the nature and requirements.
- Direct coordination was required with WPAFB and AES (electric utility) concerning primary switch location, required manholes, and electric ducts, as well as generator location in a very tight footprint. Clear direction was provided in the RFP as to who was responsible for what work between WPAFB, AES, and the contractor.
- Historic Preservation: Since Facility 20006 was historic, the team provided concept designs and proposals for presentation to the State of Ohio Historical Preservation Office (SHPO). The concept design required 3 alternatives for approval for the outdoor air intake and exhaust, window selection and large hangar door disposition. The alternatives were presented to WPAFB and then the State Historic office for review and approval. Approval was granted, and clear direction was provided in the RFP.
- Since the hangar was surrounded by thick aircraft ramp concrete, any required change to the ramp would be very expensive due to the thickness of the pavement. A detailed analysis of required parking, ATPF standoff, and how to handle the existing pavement was reviewed, and the most cost-effective solution was presented in the RFP.
Alex Burke, Energy Procurement & Environmental Sustainability Advisor, Cardinal Health Alex is an Ohio native who currently helps solves private sector sustainability and energy procurement issues with Cardinal Health. His graduate research at Ohio University explored the decision making process of energy procurement through a triple bottom line lens and enabled him to develop a small research solar PV installation on campus. After graduating he came to Columbus and worked on sustainability data software solutions with JadeTrack. He lives in Dublin, Ohio and when he is not pursuing sustainable energy solutions he enjoys reading, gardening and music. | ![]() |
---|---|
Meghan Riesterer CEM, CDSM, LEED AP, Assistant Vice President Campus Energy & Sustainability, Oberlin College Meghan's expertise in reliable, resilient, and sustainable energy systems coupled with her passion for inspiring and building sustainable organizations and strategic relationships make her well-suited to develop innovative, high-impact resource conservation, procurement, and sustainable investment strategies for Oberlin College where she leads the Office of Environmental Sustainability. She is responsible for development of the sustainable energy and utility campus infrastructure as well as implementing organizational strategic visions for carbon reduction and fostering collaborative partnerships and organizational engagement. Prior to Oberlin College, Meghan was the Director of Sustainability at the Medical Center Company, a district energy company serving thermal utilities and electricity to a hospital and university among other customers. Throughout Meghan's career she has sharply reduced carbon and created sustainable decision-making platforms and organizational efficiencies through a holistic systems thinking approach. She is a Certified Energy Manager®, Certified Demand-Side Management Professional, and LEED® Accredited Professional. She earned her Master in City Planning degree from Massachusetts Institute of Technology (MIT). | ![]() |
Ann Walston, System Director, Facility Management, OhioHealth Ann started her corporate real estate career as a project manager with Procter & Gamble in Cincinnati, Ohio. In 2003, she moved to Jones Lang LaSalle, a $6 billion real estate and facilities management firm. During her tenure at JLL, she held a variety of project management, property management and facilities related roles spanning the globe, eventually settling back in Ohio where she managed an 8 million square-foot national portfolio for a Fortune 50 company. In March 2017, Ann joined OhioHealth, a $4+ billion, not for profit health care provider based in Columbus, Ohio which serves healthcare needs in 47 counties throughout the state. As the Senior Director of Facilities Management, Ann manages the facilities and property management operations for a portfolio of over 9 million square feet, consisting of 12 hospitals and over 200 properties. In this role, Ann focuses her 200+ OhioHealth team members in supporting OhioHealth’s mission to improve the health of those we serve. Ann is responsible for all maintenance and operations across the system, including the energy management program. She chairs OhioHealth’s Utilities Task Force, a multidisciplinary system-based group whose goal is to create the most efficient and effective utility program for OhioHealth Ann is a graduate of the University of Cincinnati with a Bachelor of Science in Electrical Engineering and earned her Master of Science in Electrical Engineering from the Georgia Institute of Technology. Ann is also a LEED Accredited Professional. | ![]() |
Ryan Hoffman, PE, CEM, BEAP, LEED AP BD+C, O+M, Building Optimization Practice Director, HEAPY (moderator) It’s HEAPY’s corporate mission to build a more resilient and sustainable society that guides Ryan’s approach to improving the outcome of our project work. As Director of the HEAPY Building Optimization Practice, Ryan’s breadth of experience provides a strong foundation for leadership in offering creative and forward-thinking concepts to influence HEAPY’s projects. Corporate clients ranging from REITs, to healthcare organizations, to numerous Fortune 100 organizations, represent a large base of those Ryan has inspired over his 13 years at HEAPY. | ![]() |
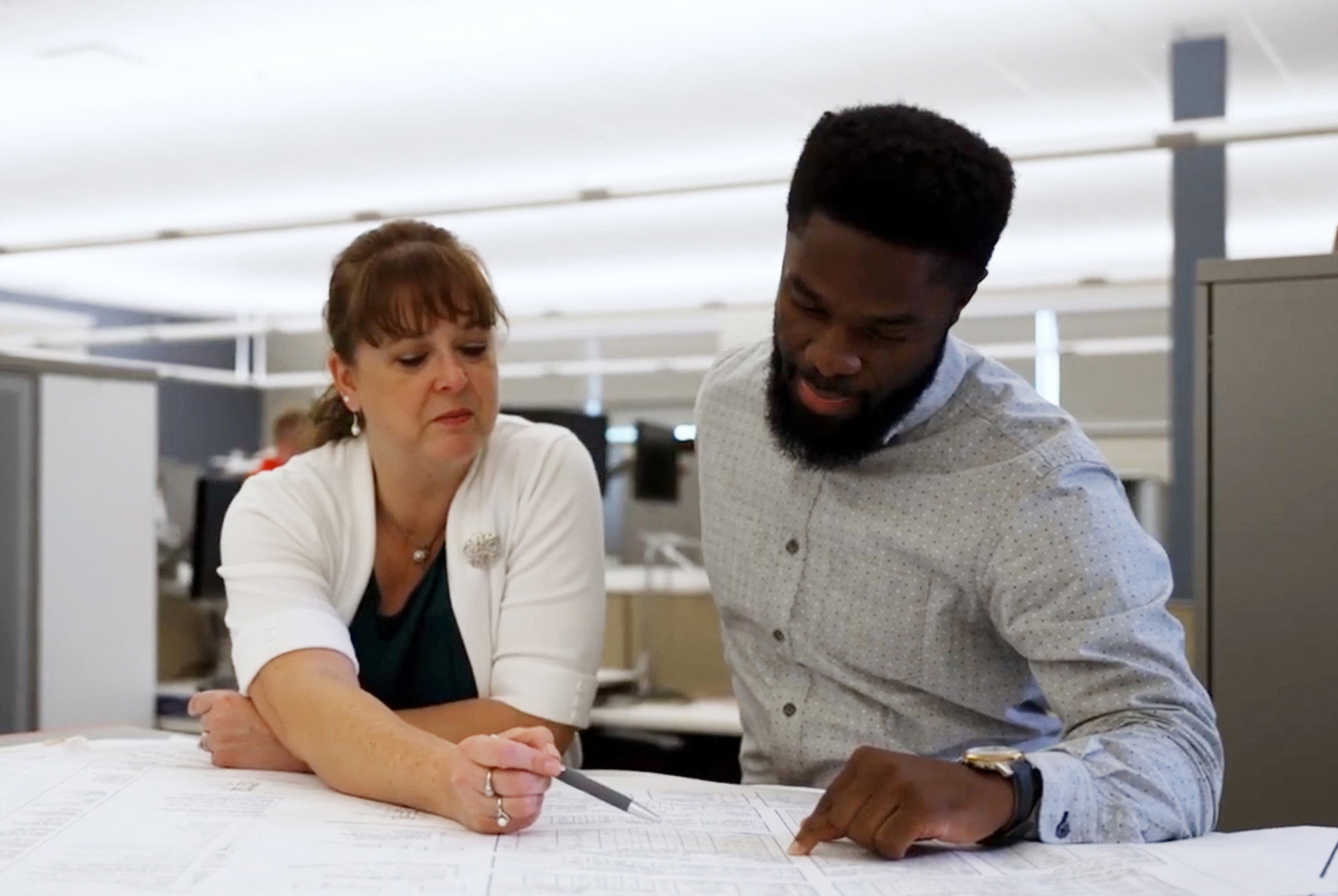
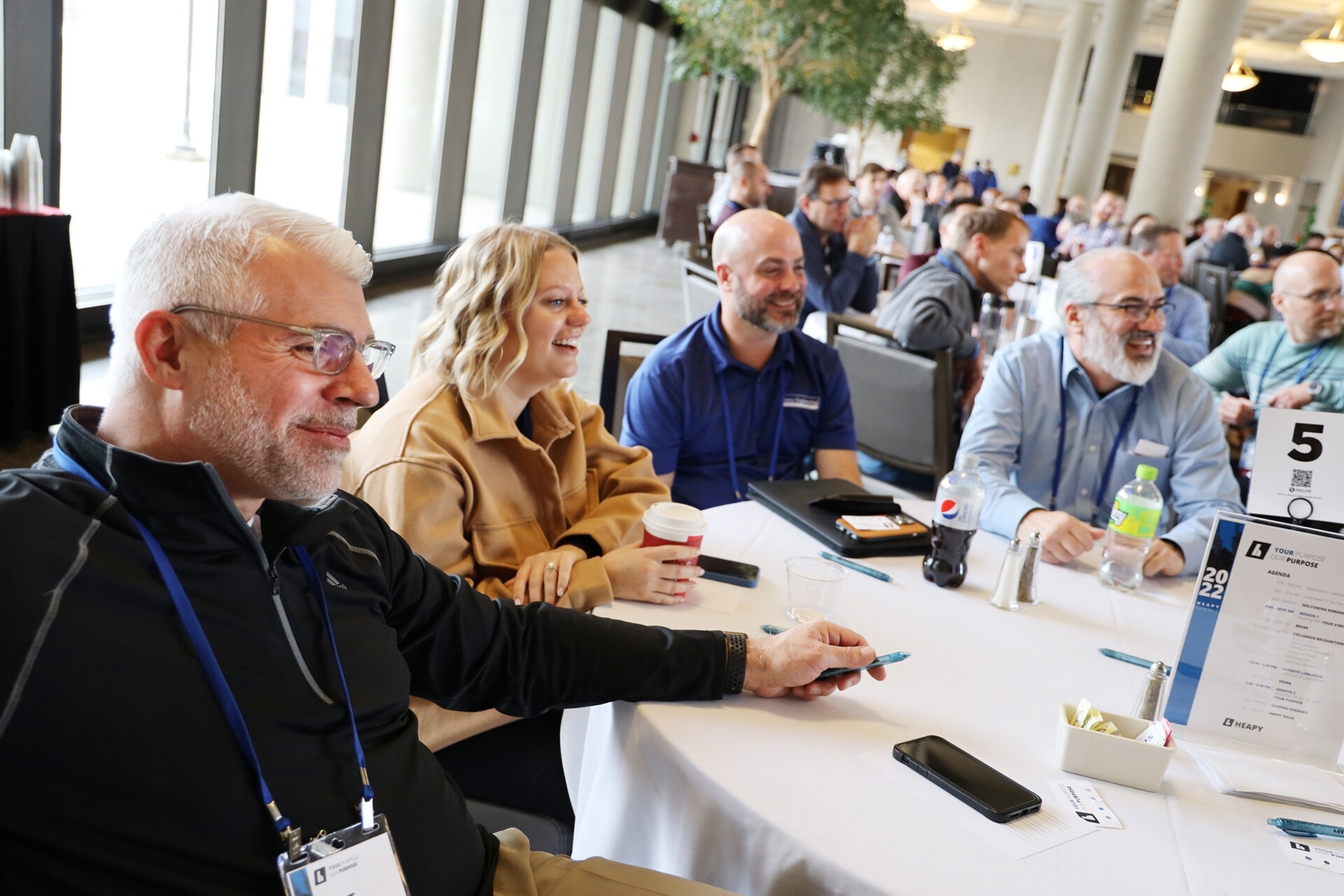