Butler University Science Complex
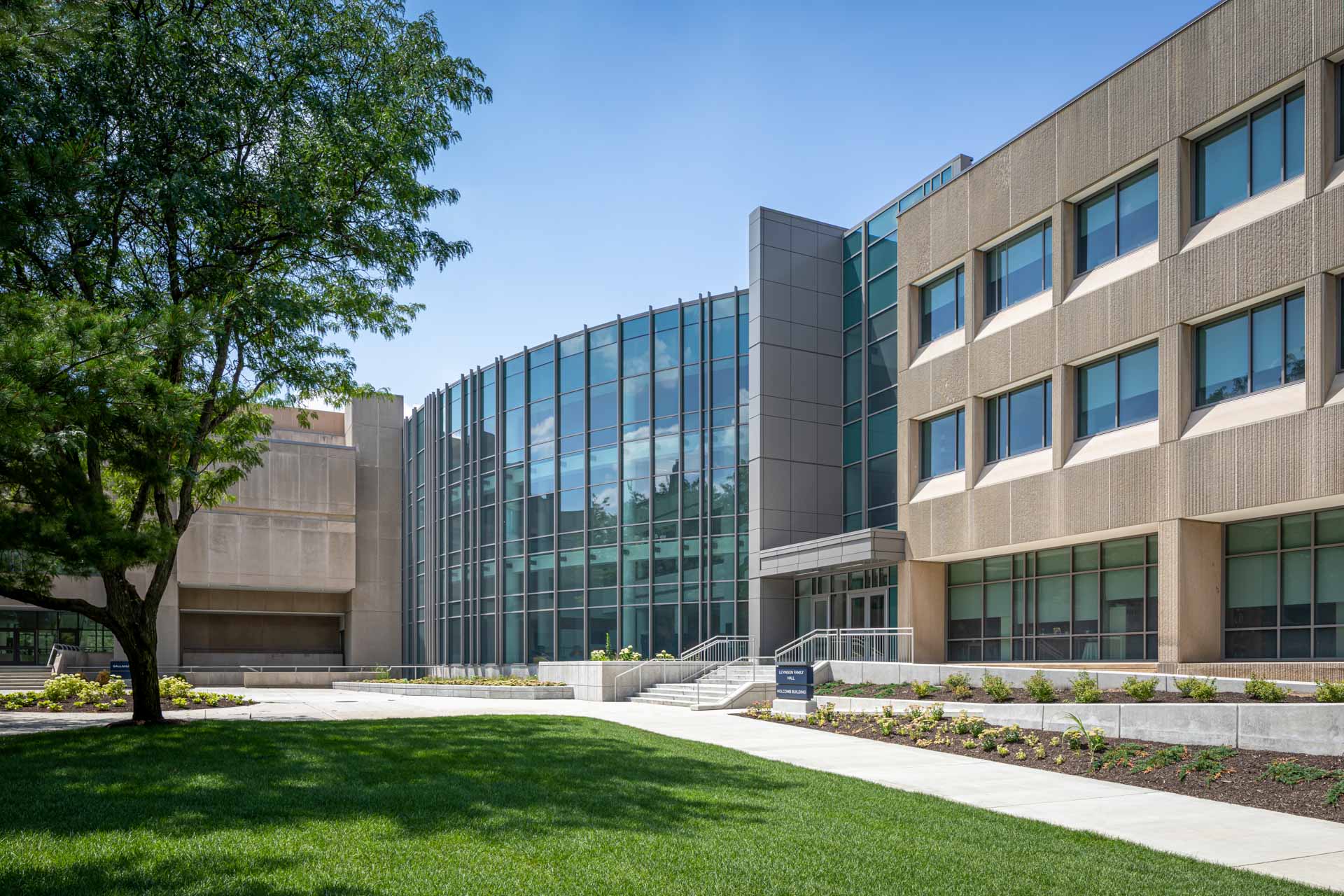
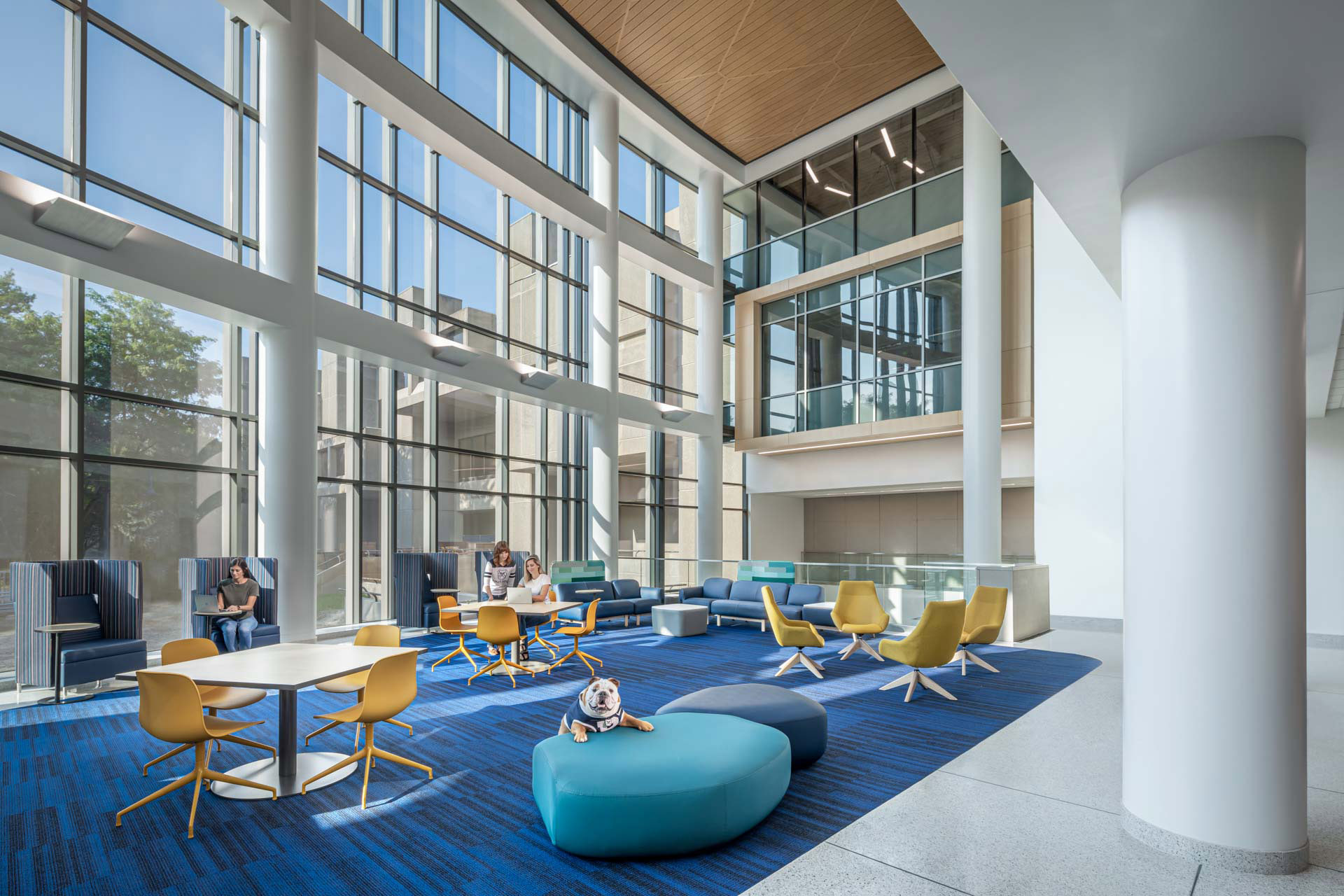
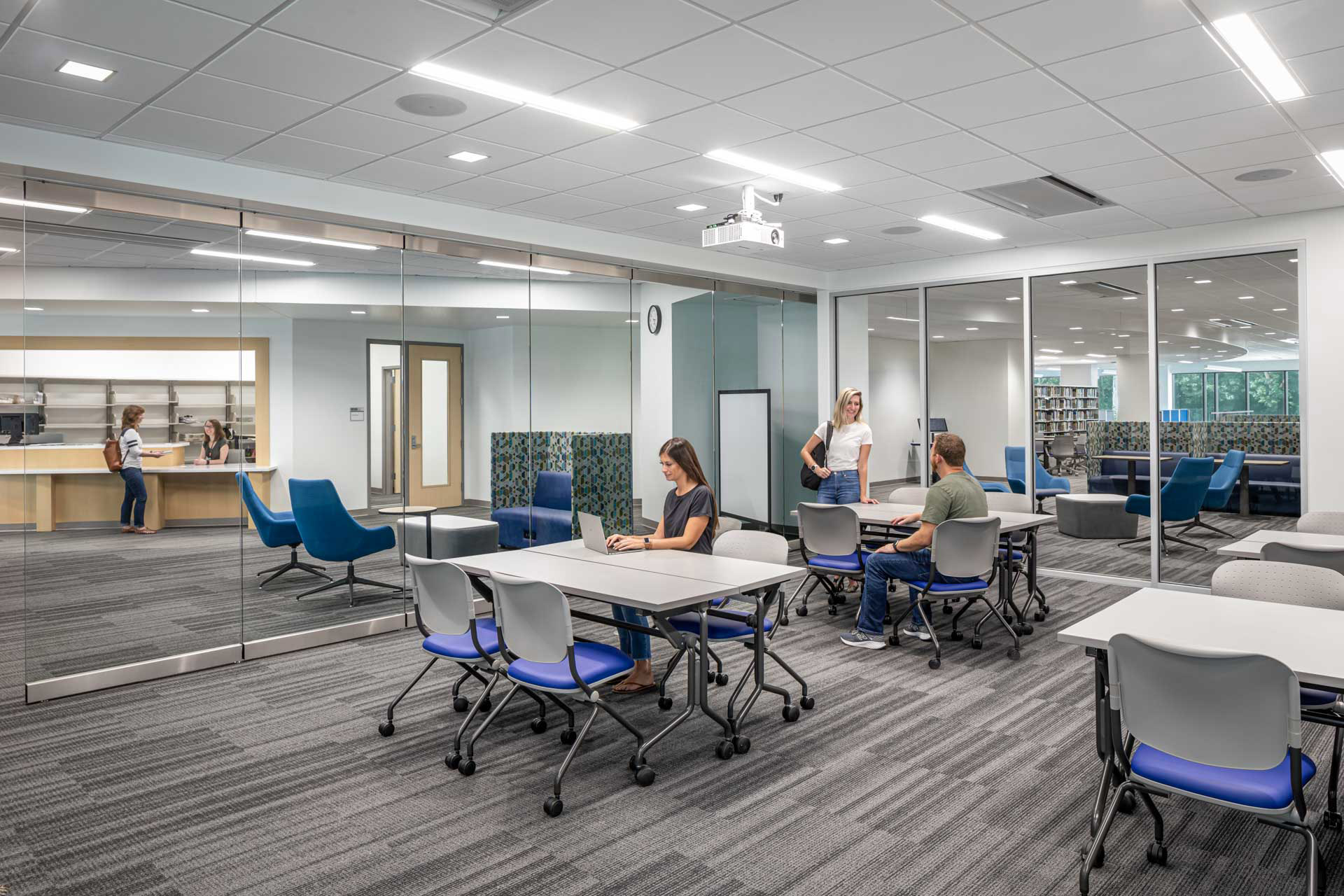
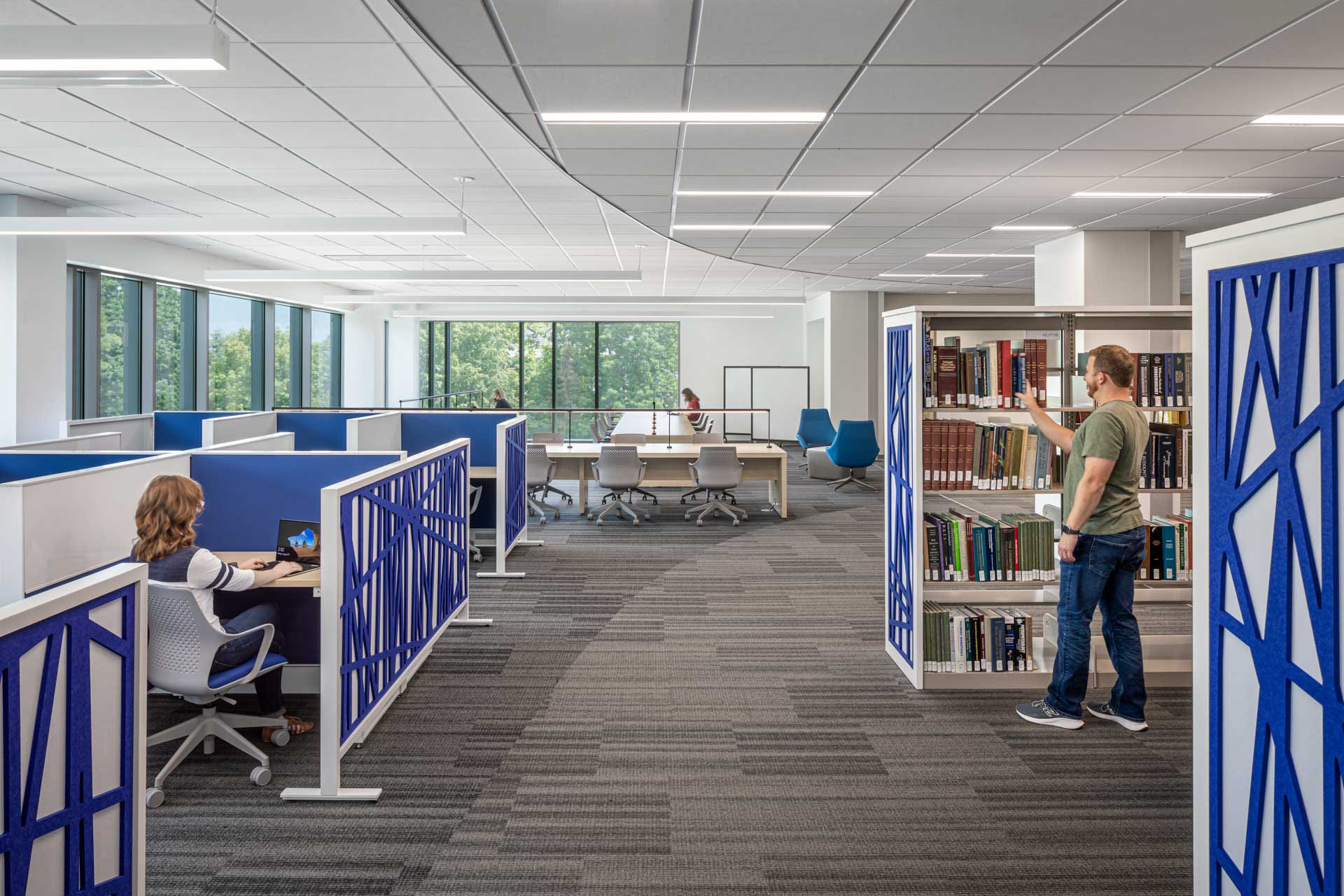
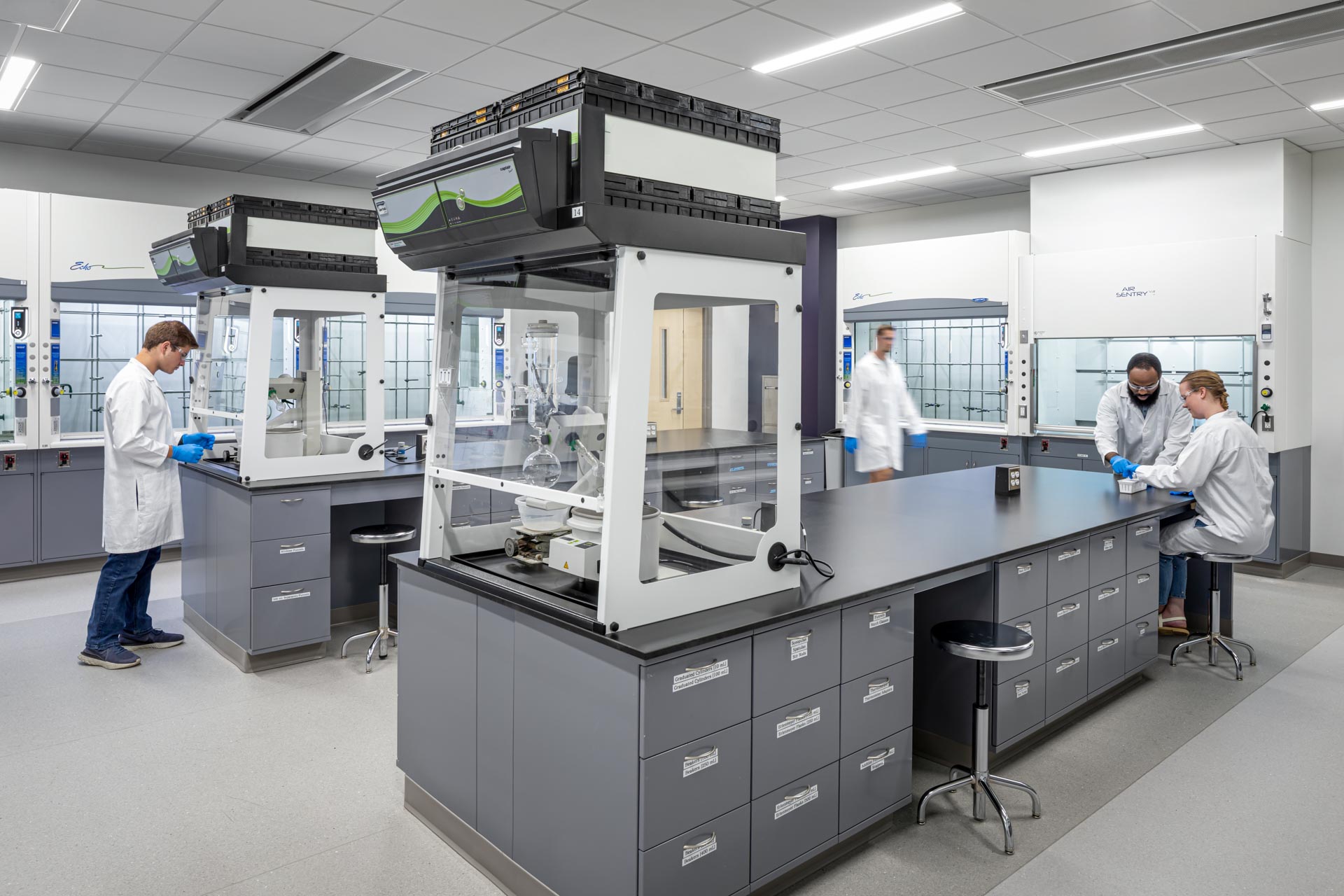
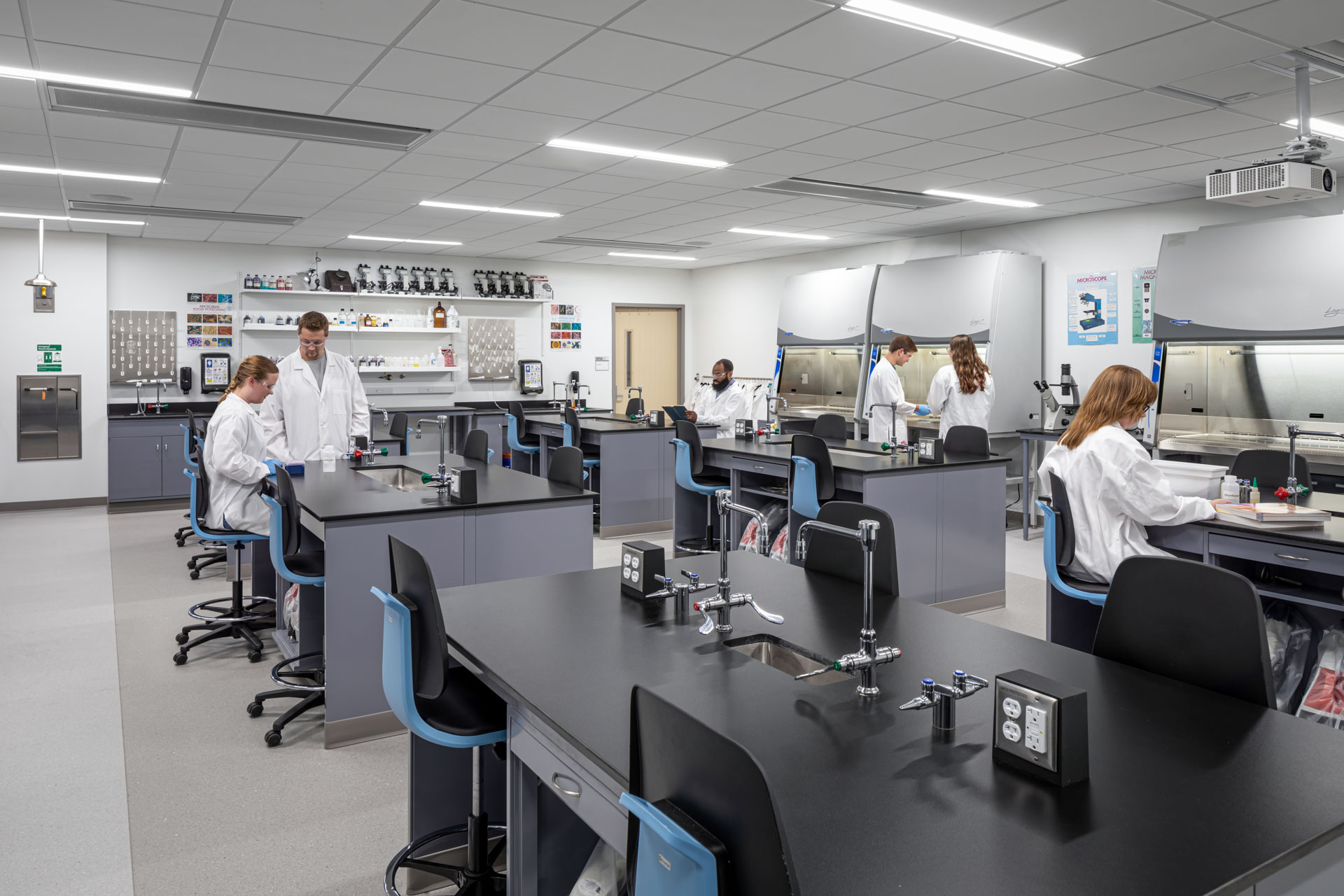
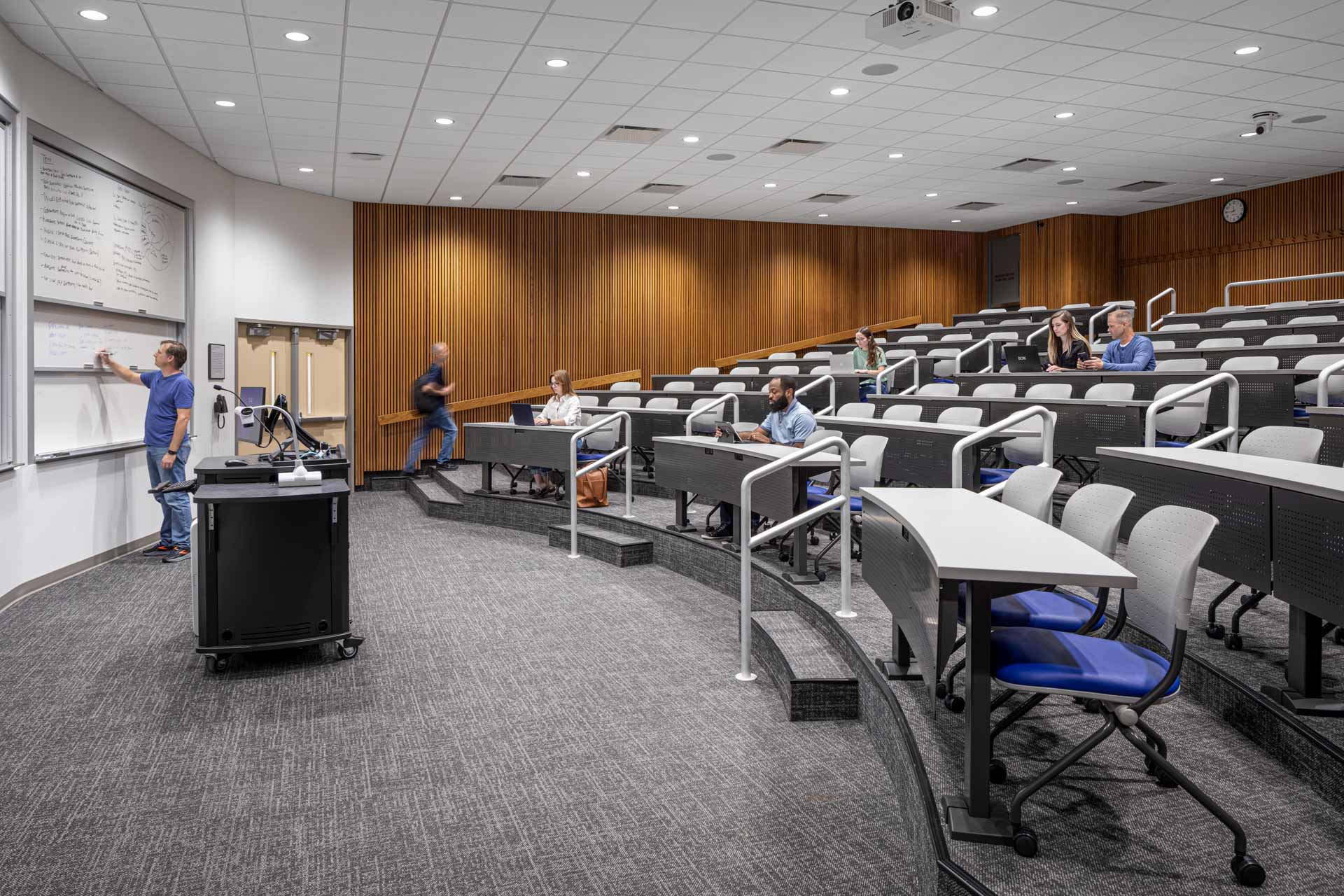
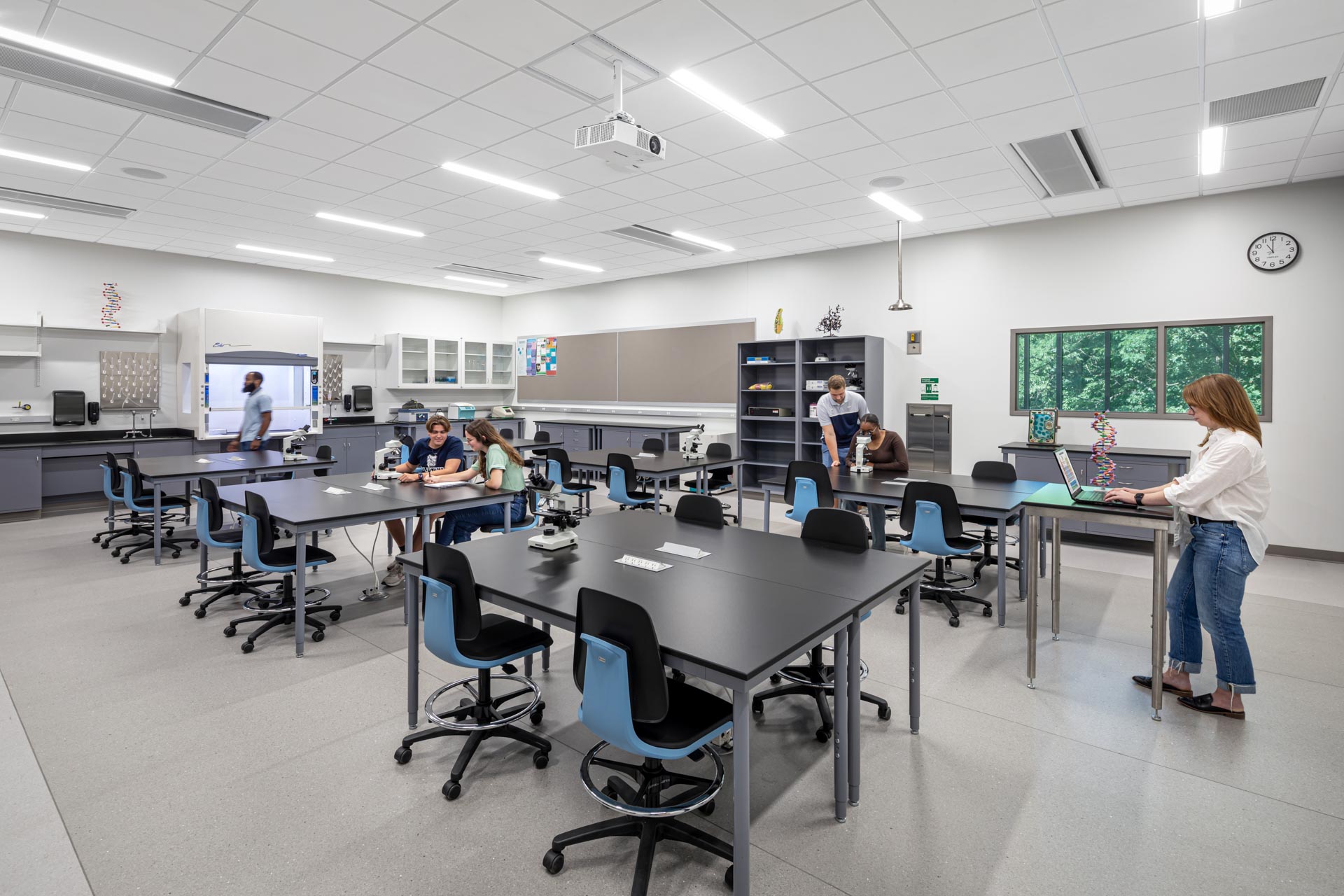
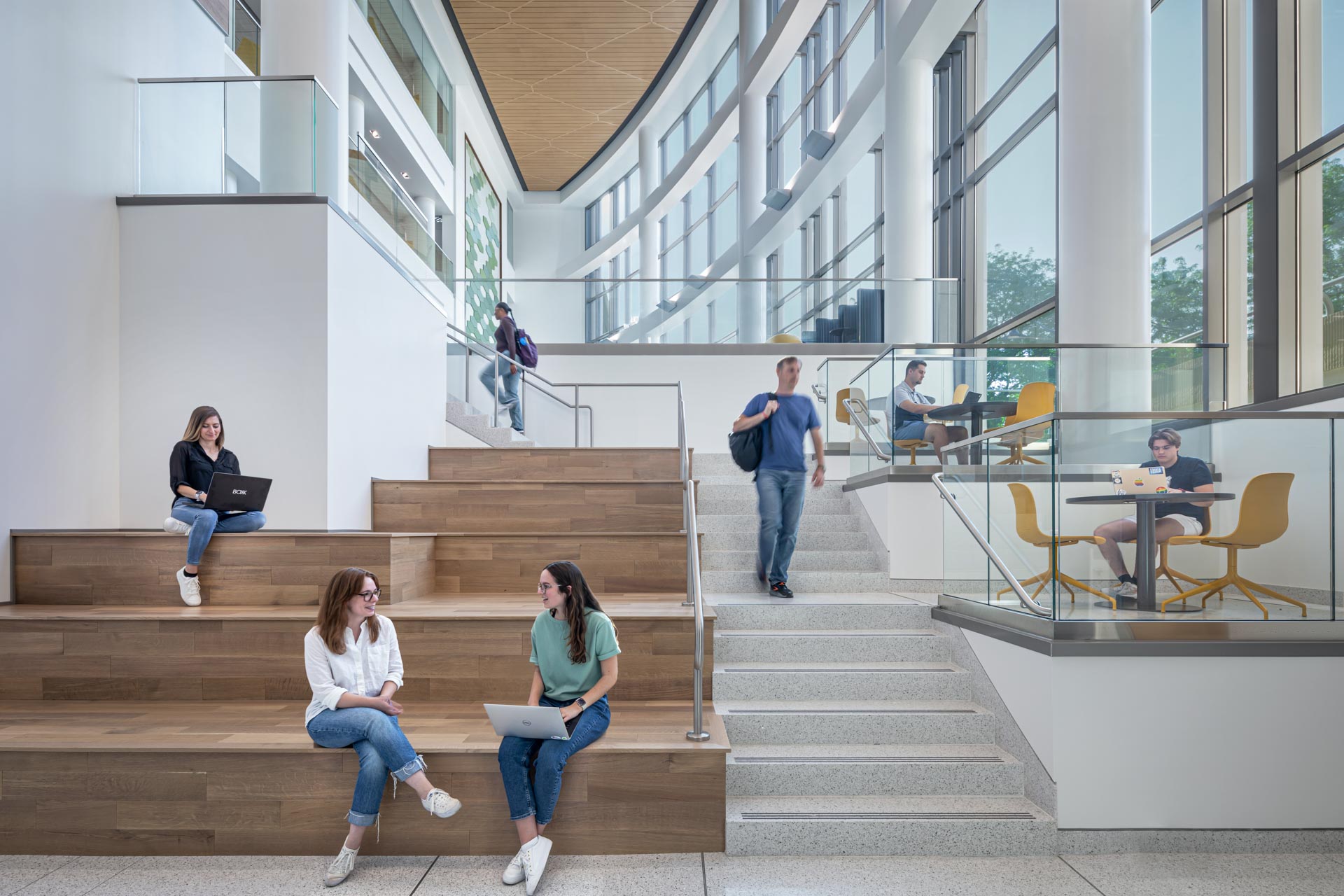
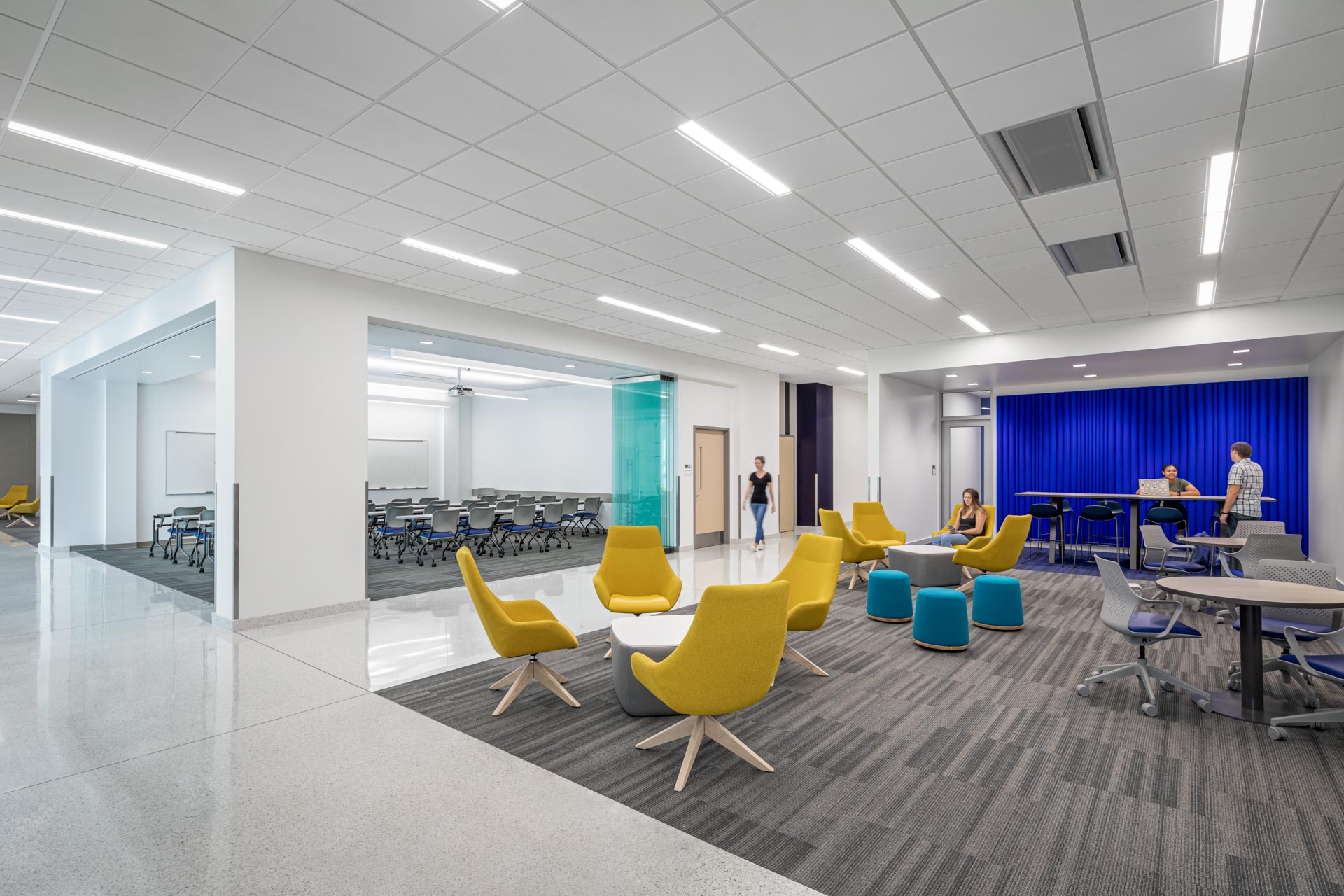
Cost $40,500,000 New Addition
$29,900,000 Gallahue Hall Renovation
$12,500,000 Holcomb Hall Renovation
$82,900,000 Total
Size 40,000 SF New Addition
120,000 SF Gallahue Hall Renovation
60,000 SF Holcomb Hall Renovation
HEAPY designed the mechanical and electrical systems for the expansion and renovation to Butler University’s Science Complex, which houses classrooms, private study areas, a library, chemistry and research labs, and common spaces. The design featured a new glass-enclosed atrium and connector building. The project was highly complex, transforming two older, existing buildings into a completely refreshed and expanded science complex to support state-of-the-art, multi-disciplinary teaching and research.
The project proceeded in three phases:
Phase I: Creation of Levinson Family Hall, a new, 40,000 SF addition connecting Gallahue Hall and the Holcomb Building.
Phase II & III: Major renovation of 100,000 SF in the Holcomb Building and complete 120,000 SF renovation to Gallahue Hall. Both received all new MEP infrastructure, as well as a new fire protection system to meet current codes and standards.
The project adhered to an ambitious timeline, while also allowing the university to offer a full curriculum throughout construction. To limit the impact on students and faculty, the project was meticulously phased over a four-year period. All construction phases had to ensure support for classes and research experiments, with consideration for noise mitigation and sound barriers, scheduled shutdowns, and access to critical spaces.
SUSTAINABILITY & RESILIENCY
The Science Complex is near the canal, which is abundant in wildlife, so fritted glass was used to minimize bird strikes. Close collaboration with the architect allowed for incorporation of shading opportunities to reduce solar heat gain in the atrium. By analyzing sun angles and peak loading, the glass frit pattern density was adjusted to provide optimal coverage. This approach improved energy efficiency and enhanced thermal comfort, while still allowing for inspiring views.
The renovation incorporated sustainable design measures such as augmented roof insulation, high efficiency glazing and insulated frames, lab exhaust energy recovery systems, enthalpy economizers, advanced BAS control sequences with lighting control, and LED lighting. Although initially targeting LEED® Silver, the project team’s early emphasis on planning and coordination enabled them to exceed expectations and attain LEED® Gold certification while adhering to the owner’s budget.
COLLABORATION & COST CONTROL
HEAPY adopted a collaborative approach with the facility staff, design team, construction manager, and installing contractors to achieve the best possible design solution for Butler University. Early planning played a crucial role in containing costs (e.g., avoiding temporary MEP systems, eliminating waste, reducing rework). To further enhance cost-effectiveness, the project employed prefabrication (23% of production hours) for many MEP utilities to reduce costs and on-site construction activities, resulting in decreased noise, improved safety, and minimized disruptions.
Contractors also heavily relied on BIM coordination and a live 3D model was shared amongst all stakeholders. This streamlined process reduced errors, enhanced early clash detection, improved access for maintenance personnel, allowed the owner to view equipment in its intended configuration, and contributed to overall cost savings.
INNOVATION
- Chilled beams were used because ceiling space was at a premium.
- Pumped coiled energy recovery system extracts energy from lab exhaust fans and redirect it back to the Dedicated Outdoor Air System (DOAS).
- A wrap-around heat pipe was used to minimize wasted reheat energy, leveraging refrigerant migration to cool and heat different sides of the coil.
- Labs included pure water systems, as well as a point-of-use vacuum system to maximize flexibility. High- and low-pressure zones were used to induce air flow instead of fans, reducing required reheat energy. Where appropriate, ductless and filtered fume hoods reduced requirements to bring in outside air.
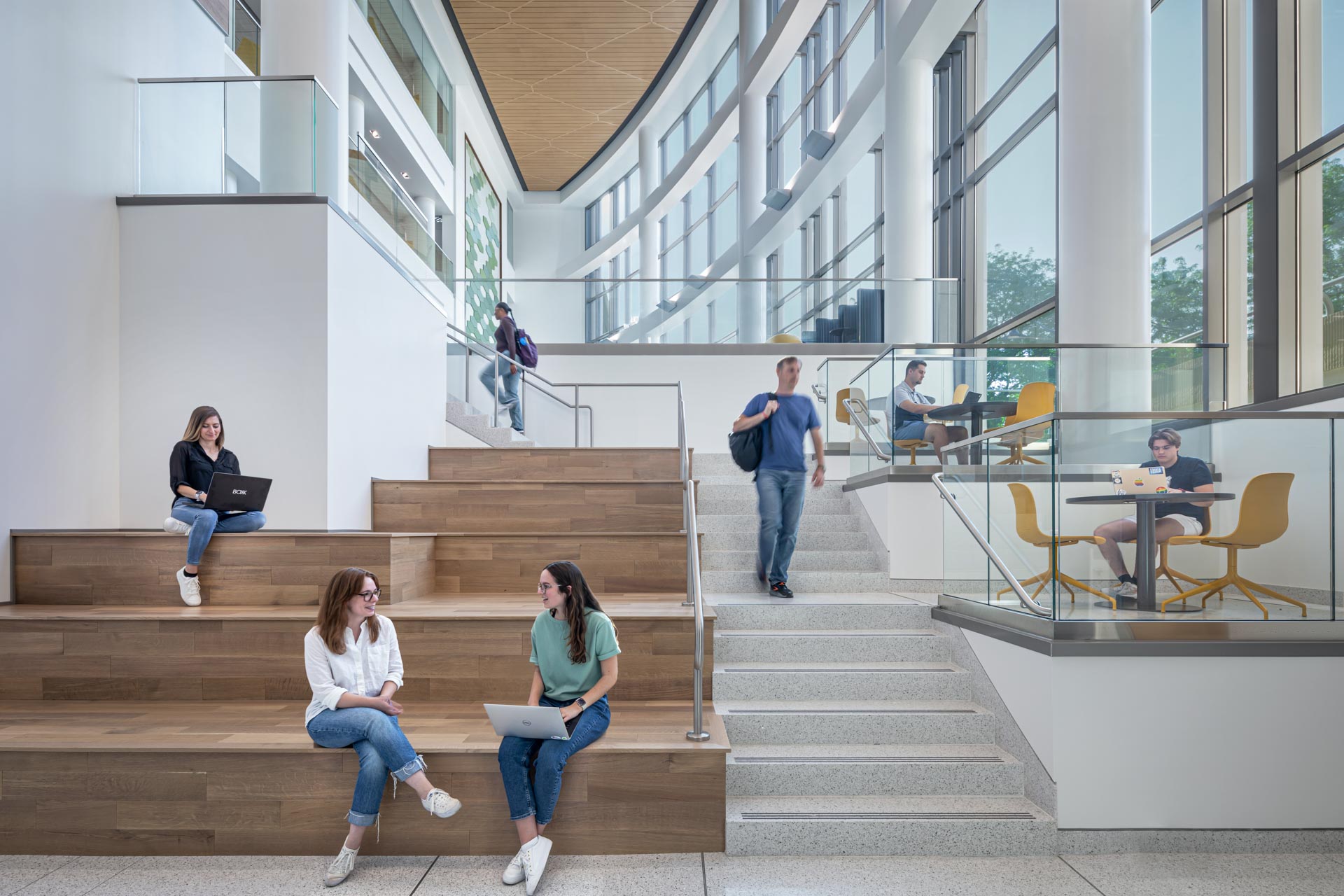
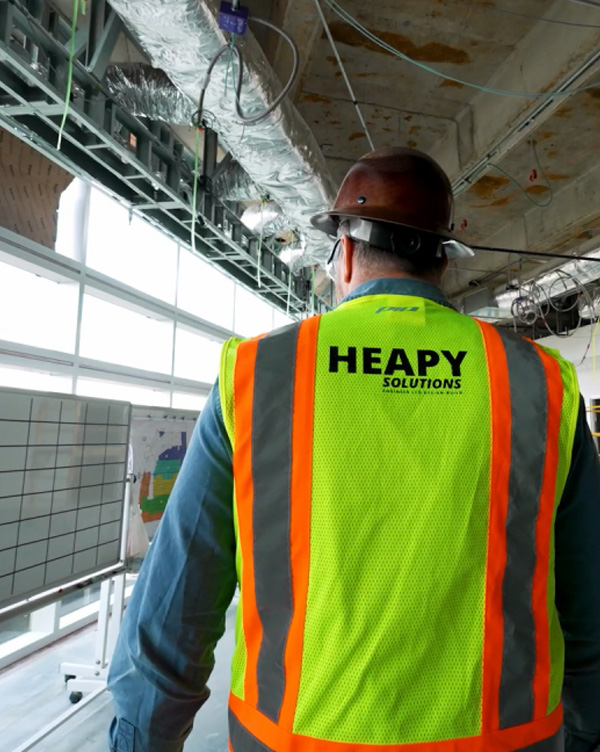